A Hammer Impact Test is also known as a Modal Test, Impulse Test, Tap Test, Bump Test or, simply, a Hammer Test. It is a method of testing that allows us to calculate the natural frequencies (modes), modal masses, modal damping ratios and mode shapes of a test structure. This is commonly done using either impact hammer testing or shaker testing. Here we are going to deal only with impact hammer testing.
What is a Hammer Impact Test?
A hammer impact test, also known as a modal test, is a way to measure how a structure responds to external forces. Imagine you have a component from a car, aircraft or satellite. You want to ensure it can withstand the vibrations caused by normal usage. This could be from driving on rough roads, landing on a runway or launching in a rocket. A hammer impact test can help determine how these components will behave under these conditions.
How does a Hammer Impact Test work?
In ideal conditions, we would impact the structure under test with a perfect impulse, an impact of infinitely short duration that results in a constant amplitude in the frequency domain. However, achieving such an impulse in real-life testing is impossible. Instead, we use a known contact time, the duration the hammer is in contact with the structure. This contact time is linked to the frequency content of the force applied.

During the test, we use a special hammer with a load cell in its tip to measure the impact force on the structure under test. The recorded response of the structure to the impact helps us determine its natural frequencies, damping, and mode shapes. This information is essential for understanding how the structure will behave under different conditions and can help us identify potential problems or areas for improvement.
Overall, a hammer impact test is a valuable tool for engineers because it allows us to better understand how structures respond to external forces and can help us design safer and more efficient structures.
<scroll down to discover all you need to know to perform hammer impact tests>
Advertisement
Some examples of the products from the CMTG brands
DJB Accelerometers
Sense

- Piezoelectric charge & IEPE accelerometers
- Instrumentation, cables & accessories
- Calibration & repair service

Prosig DATS Hardware
Capture

- Rugged, mobile data capture
- Options inc. 24-bits @ 300k samples/sec
- From 4 to 1000’s channels
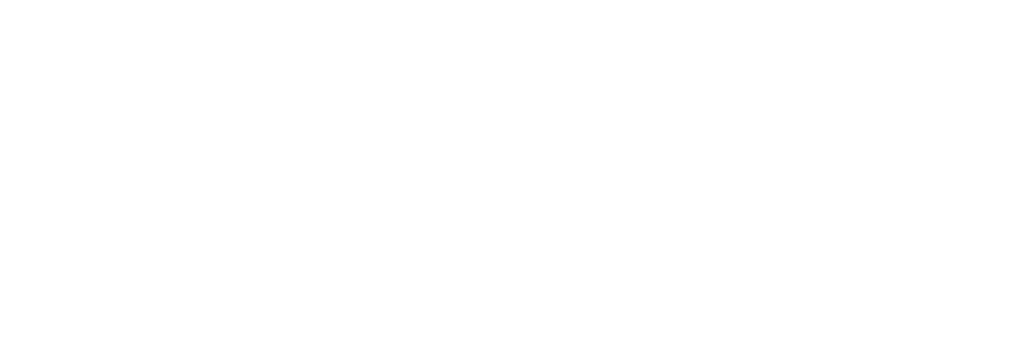
Prosig DATS Software
Analyze

- Don’t just test – gain insight from your data
- Huge selection of signal processing algorithms
- Optional application add-ons
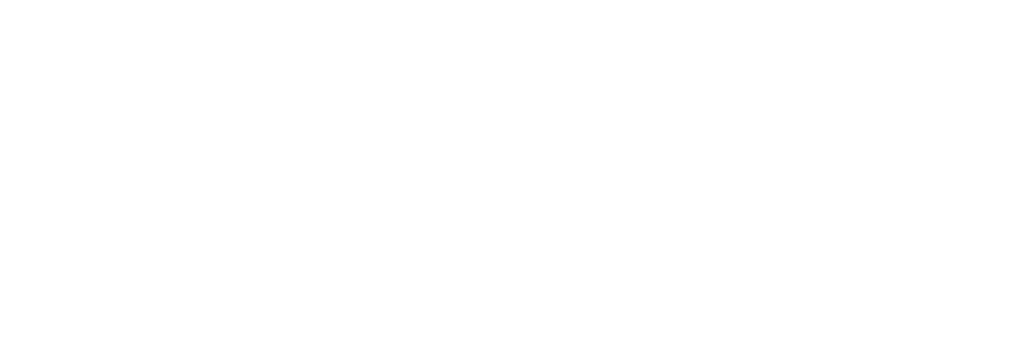
How does the test work in practice?
To test a structure, we use a special hammer to measure the force of impact and then measure the structure’s response. We need to do this at several points on the structure. There are three ways we can do this.
- First, we can put many accelerometers on the structure and hit it only once. This is a quick test, but we need to invest in many sensors and hardware with many channels to record all the data.
- Second, we can put one accelerometer in a fixed position on the structure and hit it in different places with the hammer. This is a common way to do the test, but it takes longer because we have to take many measurements.
- Third, we can hit the structure at a fixed position and move one accelerometer around to different places. This is good when we have limited space to impact the structure, but it takes the longest time because we must move the accelerometer.

What should be considered when selecting a test system?
When selecting the data acquisition hardware for hammer impact testing, it’s essential to consider the accuracy, frequency range, number of channels, sensor compatibility, data acquisition rate, software capabilities, and system portability to ensure that it meets your testing needs.
When selecting software, several important features are needed in the user interface and software. Here are some of the most important:
- User-Friendly Interface: The software should have an intuitive and user-friendly interface that leads a user through all the steps necessary to configure the test and prepare the measurement system.
- Visualization Tools: The software should provide powerful visualization tools, such as frequency response functions (FRFs), coherence functions, and mode shapes, that enable users to visualize and interpret the test results easily.
- Automated Analysis: The software should have automated analysis tools that can quickly process large amounts of data and provide results that are easy to understand. It should step the user through the measurement process and provide clear feedback at each stage. For example, audio feedback should be provided so that the user can concentrate on performing the test without referring to the computer screen at each stage.
- Customization: The software should allow users to customize the testing procedures and analysis methods to meet their specific testing needs.
- Compatibility: The software should be compatible with various systems and allow data to be exported and used with other software packages.
- Reporting: The software should have a reporting tool that allows users to generate reports quickly and easily.
The DATS-HITS package consisting of Prosig DATS-solo hardware and integrated software packages meet and exceed these requirements.
You can see an example of software used to set up and carry out a hammer test (Roving Hammer type) in the following video…
[Post updated 11th Feb 2023]
Latest posts by Chris Mason (see all)
- Rotating Machinery Vibration Analysis: Keeping Your Machines Humming Along - November 27, 2023
- Vibration Control and Isolation: A Comprehensive Guide for Engineers - November 6, 2023
- Modal Analysis in the Real World - October 6, 2023
This is my first time trying to do vibrational testing, and I was wondering if there is a way to do this all by hand using just simple data acquisition hardware and matlab. Are there any good references as to the equations necessary if you have a simple system with few significant modes of vibration?
Hello Elena,
Thank you for posting on our blog.
Yes it is possible to do this by hand.
The best references are actually on our web site, all the formula’s are included, please see here,
https://blog.prosig.com/2009/10/19/a-simple-frequency-response-function/
I need an offer to hammer test ASAP& my company in Cairo, Egypt , do you have an agent in Egypt??
Hi Walid,
Thanks for posting on our blog, I have reached out to you by email to discuss your requirements further.
James,
I am in the process of determining dynamic stiffness for certain automotive parts. We have a vibration table and a Modal Hammer for impulse excitation. What process would I take to determine the Dynamic Stiffness of these specimens. The stiffness units will be in N/mm. I understand the impact hammer will impact the part and record the force, while an accel on the part will measure acceleration and frequency experienced by the part, but how do all these components come together to calculate dynamic stiffness. Is a specific software required?
Thank you,
Chris Marsh
Hello Christopher,
Thank you for posting a question on our blog.
I would like to refer you another article,
https://blog.prosig.com/2014/04/10/how-do-we-design-or-modify-a-system-to-avoid-resonance/
This should take you through step by step the process to find the stiffness and change it.
I believe the SI unit for stiffness is N/m.
Dear Sir,
I have impulse hammer and accelerometer time data from field. I also know
the distances between source(hammer) and receiver (Accelerometer). Does it
possible to calculate the velocity of wave by using these data? if Yes, how. I do not have two
relative accelerometer data set, which is normally used literature.
Thanks in advance
Mahabir Prasad
Hi sir, Please I wanted to perform a hammer impact test but my question is this, does it matter the position one place the components? In my case, it is a cylindrical metallic pipe. If i’m to conduct the experiment, does the impact direction (x, y or z) affects the stiffness? I mean can I use any direction?
Pingback: Hammer Testing: Completely free or completely constrained? - Prosig
Pingback: Made To Measure - Noise & Vibration Blog