Prosig was contracted by Imperial Electric in Akron, Ohio to integrate a system for end of line vibration test for electric motors they manufacture. The requirement was to qualify motors under final test to verify that vibration levels are within vibration specifications. The customer requested the ability to switch between numerous motor models and apply different pass/fail limits for the different models. There was also a requirement for another test for a gearbox to evaluate the 1 times (1X) and 2 times (2X) gear tooth contact frequency. This was also an end of production line test.
In this post we will look at how we set up automated tests for their electric motors and gearboxes and the considerations given to making the test flexible and easy to use for the end user.
The test system consisted of a Prosig P8004 data acquisition system and Prosig’s DATS software.
End Of Line Testing – Motors
A simple pass/warn/fail test based on single channel overall RMS vibration levels was implemented based on the specification provided by the customer. A customized user interface was created to allow ease of testing and transducer configuration by the plant production personnel. Motor models are selected from a drop down list to set associated vibration target levels.
Figure 1 shows the user interface for setting up the transducer sensitivity and measurement parameters and designating which motor is being tested.
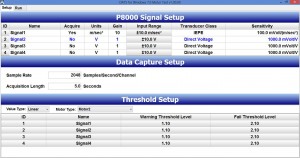
Warning and fail target levels are recorded in a CSV file and the motor test software recalls the appropriate values for the operator specified motor model. The custom user interface makes the software easy to use and minimizes operator error. The number of motor models is not limited and can be readily maintained and expanded by the customer either with the Windows Notepad or Microsoft Excel (Figure 2).
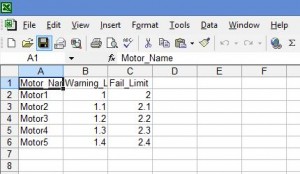
Figure 3 shows the screen displayed during data capture. The countdown timer provides feedback to the operator showing the acceleration vibration data is being captured.
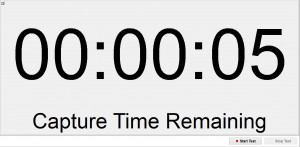
After the completion of the measurement, one of 3 screens is displayed indicating the condition of the tested motor (Figure 4).

Testing of the next motor is again started by mouse clicking on the “START” button on the screen showing condition of the tested motor.
This system is currently being used to qualify production at the customer’s Akron, OH motor manufacturing/assembly plant.
End Of Line Testing – Gearbox
This test is somewhat more involved as it requires measuring the vibration acceleration signal (g), calculating the vibration spectrum, integrating the signal to velocity (in/sec), identifying the 1X and 2X gear tooth contact frequencies and evaluating each to verify the gearbox is within specified velocity vibration levels. This test is not performed in an assembly line situation. It is a more off line test.
The gearbox is placed on a motor fixture which rotates the gears. An accelerometer is mounted on the side of the fixture and the vibration is measured for a specified time. The gearbox test uses the DATS worksheet capability to control the measurement, assess the vibration levels, and indicate pass/fail of the product.

Once the DATS software is launched it automatically launches the data capture software using a pre-defined setup file. It then makes the measurement, integrates the acceleration signal (g) to velocity and converts the units to in/sec. Pass/Fail (1X)/Fail (2X) screens are then displayed indicating the condition of the tested gearbox.
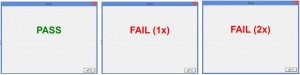
A plot of the gearbox velocity spectrum is displayed showing the target levels for both 1X and 2X and the measured velocity vibration signal (Figure 7). After the user acknowledges the Pass/Fail condition, the software asks if another gearbox is to be tested.

Conclusions
The gearbox test presented a few more challenges than the motor test, but the flexibility of the DATS software made it easy to configure it to the customer’s requirements. Both test systems are now installed and running smoothly and the customer is very happy with the results and ease of operation.
John Mathey
Latest posts by John Mathey (see all)
- Exhaust Vibration Measurement – A Case Study - March 11, 2016
- What Is Amplitude Quantization Error? - January 27, 2016
- Creating An End of Line Vibration Test System - February 25, 2015