Prosig were recently involved in the validation of a closed loop control system for an automotive pump supplier. The customer has a large number of test cells, each test cell has 8 pumps continually on test. Each pump is instrumented with a revolution or tachometer sensor, giving a once per revolution tachometer pulse. Additionally, there are various analogue transducers on each pump which measure parameters, such as pressure at the pump inlet and outlet.
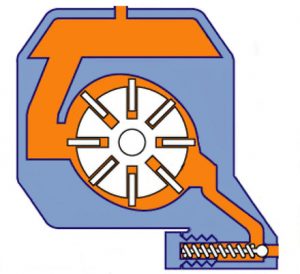
The hydraulic power is provided by a rotary pump (see figure 1). The type of pump shown is a rotary vane pump (figure 2). The pump is driven by the vehicle engine, usually via a belt. It contains a set of vanes that spin inside an oval chamber.
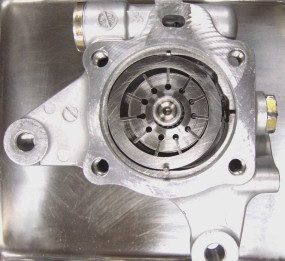
As the vanes spin, they pull the fluid from the reservoir at atmospheric pressure and force it into the outlet at a much higher pressure. The amount of pressure, and therefore flow, provided by the pump depends on the speed of the pump rotor. Since the pump rotor is driven by the vehicle’s engine, its speed is a function of the engine speed. The pump is designed to provide adequate flow when the engine is idling. As a result, the pump moves much more fluid than necessary when the engine is running at higher speeds.
The pump contains a control valve that is electronically controlled and operated. The valve control system ensures that the pressure at the outlet does not move outside a defined tolerance band. If the pressure at the outlet is too low the control valve opens and if the pressure is too high it closes.
The customer needed to validate a newly developed control system. The new system is designed to open and close the release valve a certain number of times for each revolution of the pump rotor. The magnitude and duration of these valve opening events modulates the pressure and flow rate at the outlet to the desired level for the application of the pump.
The Prosig P8000 unit fitted with analogue input channels and tachometer type input channels is used to capture and analyze all the various signals from a pump in one of the test cells.
The function of the pump’s electronic control system is to modulate the outlet pressure. To achieve this, the pump release valve has to open and close four times per revolution of the pump rotor. The opening and closing events of the valve should be at very specific times with respect to the pump rotor. That is, for each pump revolution the valve should open and close 4 times. This ensures a steady flow of fluid, but critically allows the pressure to be maintained.
To validate the customers control system the Prosig P8000 must measure the tachometer channel and the release valve opening and closing. The signals being measured are the tachometer signal and the valve opening and closing. However, the actual value movement is not being measured. As the application is to validate the control system the measured signal is the electrical signal that energizes the solenoid to open or close the valve. This signal comes from the electronic control system.
These signals must be measured very accurately in the time domain. This is a good way to measure and validate the control system for a particular pump rotor speed, since it is possible to measure the time between the tachometer pulse and the release valve opening and closing. Thus, as the position of the tachometer pulse is known with respect to the position of the pump rotor, this relationship can be deduced. The customer knows what the relationship should be from mathematical calculation and what the relationship is from simulations between the tachometer pulse and the release valve opening and closing.
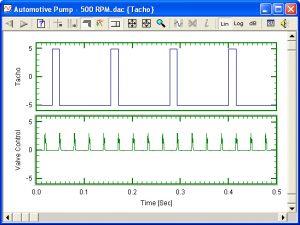
For the first data capture the pump was driven by the test cell at a speed of 500rpm and the signals captured. The actual relationship between the tachometer pulse and the release valve opening and closing from is shown in figure 3. Figure 3 shows the once per pump rotor revolution tachometer signal. The second signal is the valve control signal, this shows the valve opening and closing four times for each tachometer pulse. These opening and closing events are for very short durations, as can be seen from the time scale on the graphs.
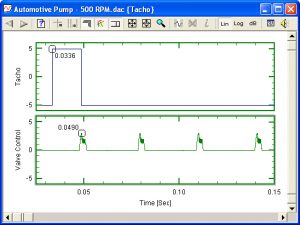
Figure 4 shows this relationship in more detail. It this case the time between the raising edge of the tachometer pulse and the point of the maximum value opening on the first event is shown using “cursor markers”. The cursor markers are a standard feature of the DATS Professional software. This clearly shows that the time between these events is 15.4 milliseconds.
The two times shown in figure 4 show that, for this particular pump speed of 500rpm, the time difference is 15.4 milliseconds. The customer was able to confirm this was as expected. However, this time relates to an angular difference. The times between tachometer pulses or the time between the pump rotor revolutions must be divided by 360 degrees. The difference in time between the tachometer leading edge and the valve control signal should be multiplied by this factor. The valve is open at some angle after the pump rotor has moved round from its centre position.
So,
tachometer raising edge time1 = 0.03346 seconds tachometer raising edge time2 = 0.15626 seconds
The time between tachometer pulses and therefore a single revolution of the pump rotor;
0.15626 – 0.03346 = 0.1228 seconds
therefore 1 revolution time = 0.1228 seconds
1 revolution time / 360 = time per degree
time per degree;
0.1228 / 360 = 3.41 x 10-4 seconds
Now,
tachometer raising edge time1 = 0.03346 seconds valve control signal time = 0.04898 seconds
therefore the time between tachometer raising edge and the first valve event is,
0.04898 – 0.03346 = 0.01552 seconds
hence the angular relationship between these two points is ,
0.01552 / 3.41x10-4 = 45 degrees
However the customer needed to validate the control system at any speed and not just at a particular speed.
The relationship between the tachometer signal and the release valve opening and closing is not fixed in time. When the pump rotor is moving very quickly the time between the tachometer signal and the release valve opening closing will be very small. When the pump rotor is moving very slowly, the time between the tachometer signal and the release value opening and closing will be larger.
However, in both cases the relationship between the tachometer signal and the release value opening and closing four times will be fixed in the angle domain. That is the control system should open and close the release valve four times equally across a single revolution of the pump.
A small complication arises since the control system is actually active, so it will vary the angle very slightly with respect to rotational speed.
However, the customer knows the angular relationship as a function of speed. As stated previously, the test is to validate the control system and make sure it’s functioning as expected.
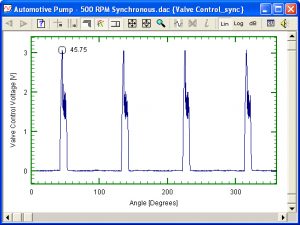
In order to validate the control system the captured data can be displayed in the angular domain using the DATS Professional software. Figure 5 shows the valve control signal at 500rpm in the angle domain.
Since it is possible to visualize the data in the angle domain, there is no need for the comparison between two signals.
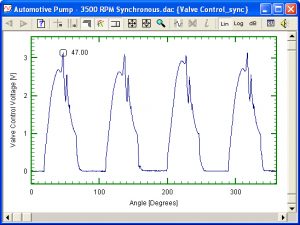
Figure 6 shows the angle at a higher speed – 3500rpm. In this case the maximum peak is more difficult to pick out as it is much faster. The graph clearly shows the maximum point at 47 degrees. The DATS professional software peak detection software is optimized for this sort of complex analysis and detection.
Using our first method, the data is captured and shown in the time domain. The tachometer signal is shown with respect to the valve control.
Using the second method, the data is shown in the angular domain. There is no tachometer signal shown, only the valve control with respect to the tachometer signal.
The first case requires that the sample rate is set so that the highest frequency present is captured and retained. In this case the Nyquist theorem applies. The Nyquist theorem states that the sample rate must be at least twice the bandwidth of interest. Therefore the customer must know the frequencies of interest before the data capture.
In this case the highest possible pump speed was 4000rpm. The tachometer transducer gives 1 pulse per revolution and therefore the maximum is 4000 pulses per minute. This equates to 67 pulses per second, or 67 Hz. But the Nyquist theorem states that we should sample at least twice this, at 133 samples/second. However, using the value of 133 samples / second for signals like this could result in serious under sampling. There are three reasons for this.
First, the valve control signal runs at four times this rate. We know this because the valve is opened and closed 4 times per pump rotor revolution. Therefore we should be considering 133 x 4 = 532 samples / second.
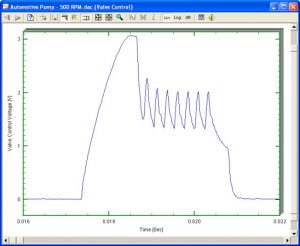
Secondly, the dynamics of the valve should be considered. As can be seen in figure 7 the valve control signal actually has high frequency content itself. This can be clearly seen between 0.019 seconds and 0.021 seconds.
The length of each of these short impulses is approximately 239 microseconds.
Therefore, the frequency content of these high frequency spikes is related by
f = 1 / t
therefore
f = 1 / 239 microseconds f = 1 / 239x10-6 seconds f = 4166.67 Hz
So to safely capture this data we should sample at a minimum of twice this frequency.
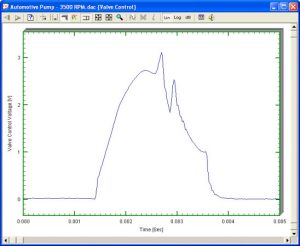
Checking the higher speed data captures for the same phenomena reveals, as expected, much higher frequency content (figure 8).
This can be seen between 0.0025 and 0.0031 seconds.
The time of these short impulses is 199 microseconds.
Using the same relationship
f = 1/199x10-6 seconds f = 5000.0 Hz
Again at least twice this rate should be used, so now we have a minimum sample rate of 10000 samples / second or 10k samples / second.
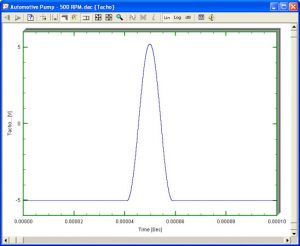
Thirdly, we must consider the dynamics of the tachometer signal. Although as discussed the tachometer has a maximum repetition of 67 times per second, this does not give a complete and full picture of the dynamics of the signal. Shown in figure 9 is a tachometer pulse in great detail.
Although this event happens some 67 times per second, the event itself lasts only 20 microseconds.
This means the frequency content of the tachometer pulse is, again using,
f = 1/t
therefore
f = 1/20 microseconds f = 1/20x10-6 seconds f = 50000.0 Hz
As previously discussed, to capture this 50000 Hz event a sample rate of at least 100000 samples / second must be used.
Now that the signals are fully understood it is possible to see what sample rates should be used for a test such as this.
The tachometer signal must be sampled at a minimum of 100,000 samples / second.
The valve control signal must be sampled at a minimum of 10,000 samples /second.
The Prosig P8000 supports sample rates of up 800,000 samples / second. Importantly it also samples each channel synchronously. As with all rotating machinery analysis multiplexed equipment is not acceptable.
Displaying the data in the angular domain, as discussed in the second of the two methods, is more complex. If this sort of display is required then the sample rate of the tachometer channel and valve control signal must be at the same highest rate. In this case, at least 100,000 samples / second. This is to ensure that the angular domain valve control data can be displayed accurately with respect to the tachometer channel in the angle domain.
James Wren
Latest posts by James Wren (see all)
- What Are dB, Noise Floor & Dynamic Range? - January 12, 2024
- How Do I Upsample and Downsample My Data? - January 27, 2017
- What Are Vibration, Torsional Vibration & Shaft Twist? - November 8, 2016
Thanks for the PDF file. It is really informative. Kudos to you.