HVAC (Heat Ventilation Air Conditioning) units are devices used in various applications, such as cars, buildings, aircraft etc. They facilitate the transport and conditioning (heating, cooling, changing of humidity) of gaseous masses. Ideally, this conditioning should be performed without creation of sound or noise. However, solving airflow instabilities in HVAC is not trivial since engineering topics like fluid dynamics, acoustics, structural and rotational dynamics are involved.
The Test Setup
The data analysis example covered in this note shows how Prosig’s DATS software is used to measure signals, process data in a logical way, solve the practical issues and obtain working solutions.
Here the focus is on the joint analysis of signals from acoustics, pressure sensing and rotational quantities. For the latter, a tachometer signal, consisting of individual pulses from the ten blades of a blower inside the HVAC unit is used. It is picked up by a laser tachometer.
Therefore a counter/timer based channel is acquired. At the same time a set of analog data acquisition channels is captured. This measures acoustic pressure information from microphones (sound pressure level, SPL) and wall pressure level sensors (WPL) mounted at various locations in the duct of the HVAC unit.
Initial Results
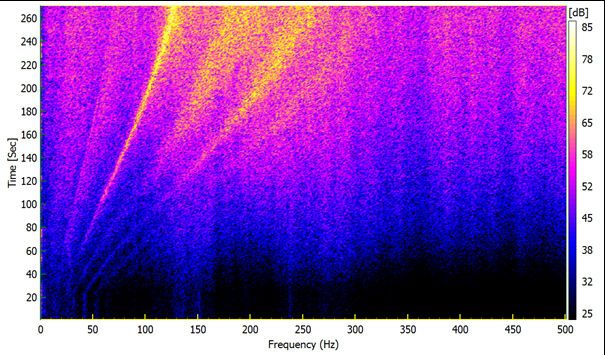
Figure 1 shows the SPL spectrogram in the usual fashion. The horizontal axis shows the frequency information. The vertical axis shows the elapsed time for a blower run-up. The resulting analysis data shows sound pressure amplitude as color coded information from a so called hopping FFT (Fast Fourier Transformation).
Initial observation could lead to the impression that plain vanilla order contributions can be spotted.
The Order Domain
However, a more in-depth analysis shows more. By converting data (from time domain) to synchronous domain using the DATS analysis tools non-integer shaft order contributions are revealed (Figure 2). Specifically, a strong order contribution, just below order 1.9, and broader contributions around order 2.7 and 3.6.

With the DATS range of analysis tools it is straight forward to carry analysis into the angular (or order) domain. The phenomena may be looked at in another very powerful visualization. That is, segmented in order domain, by setting up a revolution spectrogram. This shows data as consecutive 360° rotational angle slices for the run-up.
Any attempt to perform such a visualization with time domain data alone would be futile within reasonable amount of time devoted for data analysis!
Visualising the problem
DATS provides the ability to visualise the the physical phenomenon right away. By performing appropriate band pass filtering of synchronous domain data (centered around order 1.8) and using the previously mentioned visualization sound pressure level (SPL) and wall pressure level (WPL) data are shown in Figures 3 and 4. Observe the level differences of SPL vs WPL.
Strong pressure surges propagating along the fluid path of the HVAC unit can be spotted. This is a phenomenon originating from a non-uniform movement of gaseous fluid masses by the rotating blower.
The data representation with stacked up consecutive revolutions clearly reveals that about less than two (about order 1.8) cells are forming during one blower revolution and propagation through the scroll of the blower takes place during about ten blower revolutions (this is known as “rotating stall”).


Conclusion
DATS data analysis software is a powerful toolbox for its many diagnostic algorithms alone. In addition, the worksheet style of handling and processing data, and the possibility to concatenate analysis steps gives a professional engineer possibilities that many other programs are lacking.
Latest posts by Prosig (see all)
- Vibration Measurement Techniques: A Comprehensive Guide - August 30, 2023
- Tools for motorcycle dynamics analysis - November 3, 2022
- DJB Instruments Ltd joins Prosig as part of Condition Monitoring Group Ltd (CMG) - September 29, 2021
Did you also try to analyse the number of rotating stal cells and their change in duration and pressure gradient with regards to fan operational speed to be able to draw conclusions regarding fan operational performance?
Thanks for your question, Philip. This post was written by a long time Prosig partner. We will pass your question along and see if we can get you an answer.
Hello Philip. To summarise the response from the author of this article –
“I looked into the issue way deeper that the customer did (hope this does not sound bold) as they were annoyed by the overall SPL and I was puzzled about the physical phenomenon, cause and mitigation. Therefore I used about 14 wall pressure sensor positions along the path of the air masses to be accelerated (pressure build up etc) in order to get the big(ger) picture. And, yes, I found the physical position where the fluid restructures and these cells evolve and propagate. In fact again old analysis techniques were used (provided by DATS) which are all the cross correlation tools, again in time or revolution domain. By this it is possible to sense the propagation direction of the cells, origin and location (as they need not have to fill the air channel in total) all by using the stationary wall pressure sensors. So looking into the data, correlating, some laser vibrometer measurements (even on the blades through a laser-type AR coated window) physics unveiled. And then, the solution, which was a slight modification in the surface structure of the duct, made the “ghost vanish”…”